産学共同で「点検ロボット」を製品化
老朽化した社会インフラと向き合う
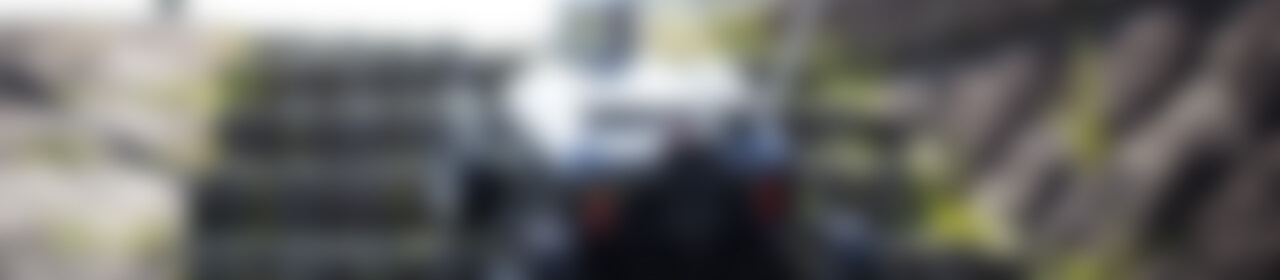
社会の「困りごと」に挑む
老朽化したインフラ対策に産学で挑戦
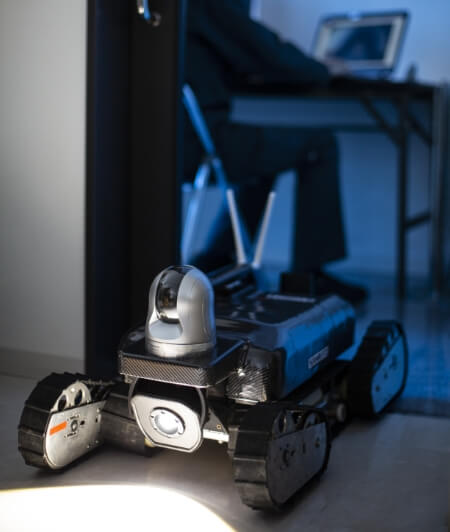
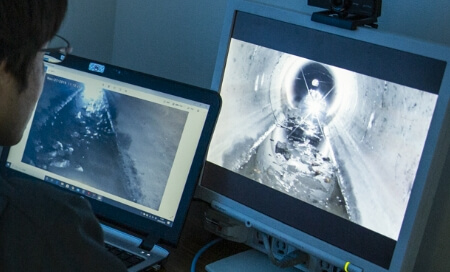
ただし、サンリツとしては、最初からロボット開発に絞り込んでいたわけではない。自社で開発し、蓄積した技術をどこで活かせるのか、さまざまな分野を検討していたと高倉は言う。
「ウチが得意なのは、計測制御のコンピュータ技術です。これを応用して最終製品を作りたいという構想は、以前から社内で持っていました。計測制御のコンピュータに、センサーと駆動メカを付ければロボットができますが、最初からロボットを目標にしていたのではありません。
2010年頃、まだ自動化が進んでいない非製造業の分野、例えば医療とか介護とか、あるいは農業といった分野のマーケティングをしたり、産学連携プロジェクトや自治体の実証評価に参加したりと、次の展開に向けたリサーチを重ねていました。
そんな時に、インフラ老朽化による点検個所の増加、それに加え頻発する災害と少子高齢化による対処のために、国土交通省を中心に、新しい点検技術が求められるようになったんですね。
国交省と経済産業省が公募したロボット現場検証事業に奥川先生が手を挙げられて、メカ作りの得意な会社や道路保全点検会社を含めたコンソーシアムを組みました。ウチも誘われて TPIP などのコンピュータ部分を担当することになったんです」
自分たちの技術が役立てられる最終製品を探していって、最初に出会ったジャンルが点検ロボットだったというわけだ。
こうして始まった産学共同のロボット開発だが、開発にはまとまった資金が要る。自治体が設定していたロボット関連の助成金を受けるには、事業化が条件となっていたことから、事業会社であるサンリツが前面に出て、開発の中心を担うこととなった。
「実証」から「製品化」への遠い道のり
しかし、産学共同でプロジェクトが始まってみると、簡単には進まない。大学の研究室で機能や性能を「実証」するためのロボットと、企業が事業として「製品化」し、実際に社会で使われるロボットとでは、モノ作りの考え方やアプローチが大きく違っているからだ。
その典型例が図面の作成。大学の研究用ロボットは、学生たちが、その時々で手作りし、改良を重ねていくので、いま目の前にあるロボットの図面は、どこにも存在しない。ロボコンに出場する機体などは1機しか作らないし、大会1回分の耐久性があれば、それで十分だからだ。
製品の開発には、機能や性能を確かめる「実証」、実際に使えるようにする「実用化」、事業として企業に買ってもらえるようにする「製品化」の3段階がある。レスキューロボットの経験が豊かな奥川研究室では、比較的「実用化」を意識したロボットの開発を行っていたが、それでも「製品化」への道のりは遠かった。
さらに課題だったのは、サンリツ自身の経験不足。コンピュータ屋であるサンリツにとって、メカ部分も含めたロボット全体のインテグレートは初めての経験だ。しかも、ロボットが相手にするのは産業用機器ではなく、土木ジャンルの現場。手探りで学ばねばならないことが次々に現れた。
全体設計を担当する三浦貴彦は、開発をスタートして初めて分かったことがたくさんあるという。
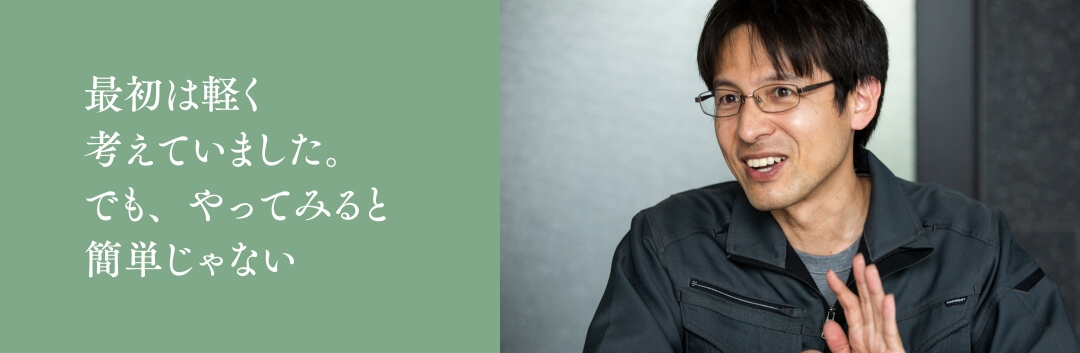
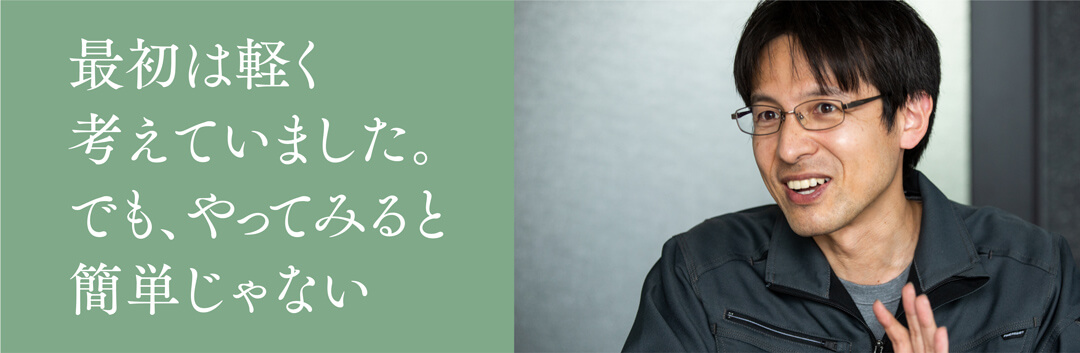
「配管の中の点検は、距離センサーを付けて計測すれば分かるだろうと最初は軽く考えていました。でも、やってみると簡単じゃない。求められる精度に対してズレ幅が大きいし、使う場所が変わるとズレ幅も変わってくる。
なぜ、ズレが起きるのか、センサーに影響を与えるパラメータを実験で確かめていって、次は影響が出ないようなセンサーの取り付け方法、使い方を探っていくんです。
距離センサーは、配管内のキズを探すために使うんですけど、キズの大きさはある程度なら画像でも確認できる。しかし、キズの深さまで測れるかどうかは、センサーの使い方、組み合わせ方しだいです。
そもそも、サンリツはコンピュータを通じてデータを収集するのは得意ですけど、センサーで収集したデータを測量や計測で活用できる形に起こすのは初めてです。統計手法を用いて意味のある数字を抜き出すノウハウを獲得するのに苦労しています」
メカを担当する三浦洋靖は愛知工業大学の出身。現在は、同校奥川研究室の客員研究員を兼ねる。ロボット開発に携わりたくて転職してきた。
三浦洋靖が開発に苦心した1つが、防水・防泥構造にすることだった。
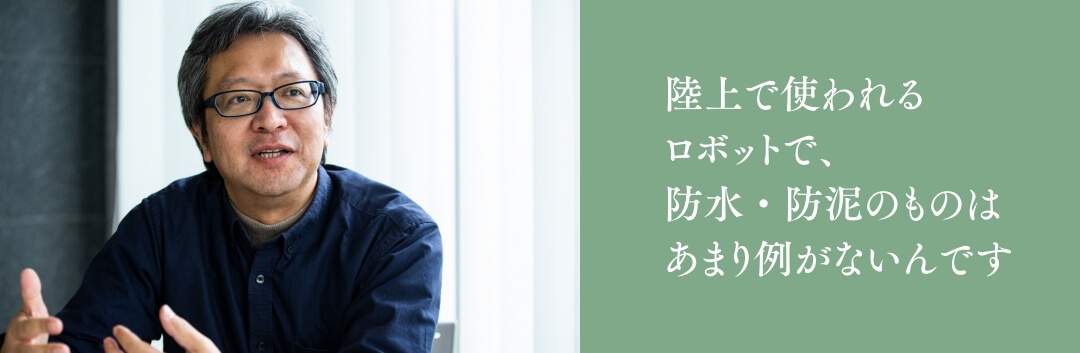
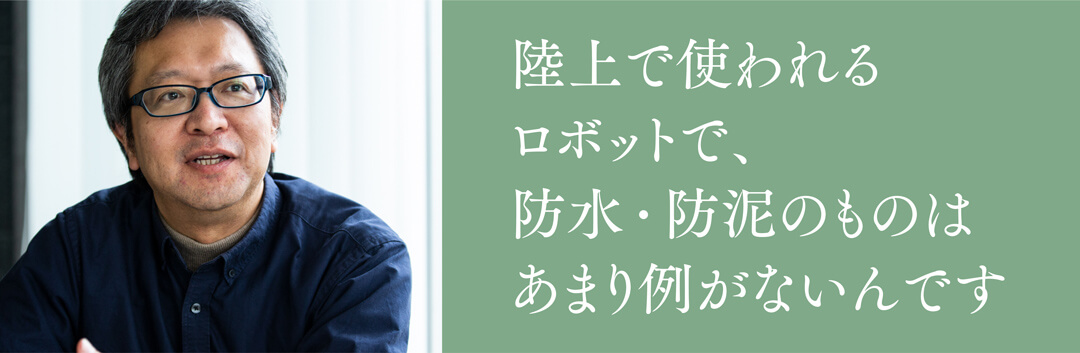
「水中ロボットならともかく、陸上で使われるロボットで、防水、防泥ともに対応しているものはあまり例がないんですね。でも、想定している排水管という使用環境を考えると、当然必要になってきます。
防水構造にすると、機構が複雑になりますし、製造の手間もかかる。試行錯誤するうちに、防水のポイントが分かってきて、必要な部分だけを密閉された防水ブロックの中に収めるという手法を採りました。いまのモデルは、非常に簡単な構造ですけど、水没しても大丈夫です。
排水管の中には泥も溜まっていますから、その対策もしました。ロボット内部に泥を入れないように作ると、もし入ってしまった時には出ていきません。逆転の発想で、泥が入ってもすぐに抜けていく構造にしました。
今後は、量産に向けたコスト削減や、メンテナンス性の向上が課題ですね。特にゴム製のクローラベルトは、消耗品なのに、二重構造の特注品で価格が高いですから」
2020年春に、やはり愛知工業大学の出身で奥川研究室から入社した開発一部の渡邊彩夏は、大学1年生からレスコンに出場したほどのロボット好き。最近では、レスコンの運営スタッフを務めている。入社までは研究室側で点検ロボットの開発に携わり、“受動適応サブクローラ”の制御を担当してきた。
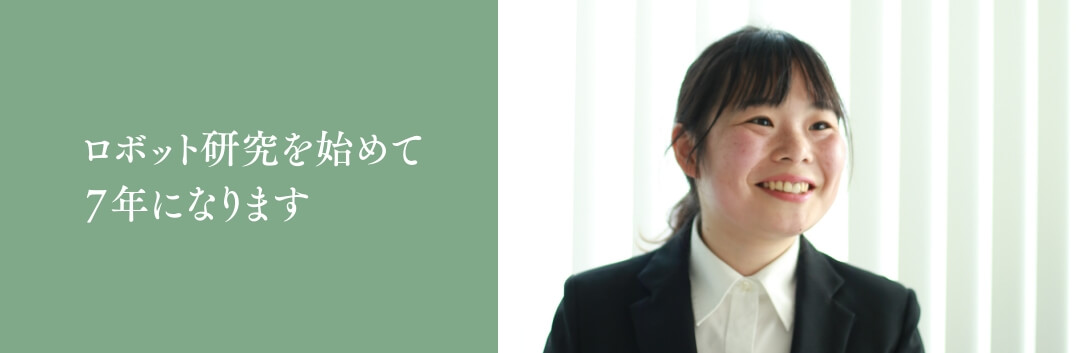
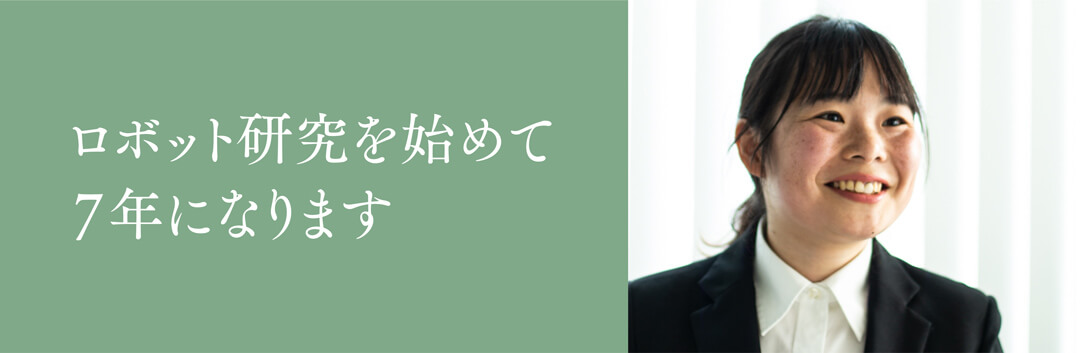
「ロボット研究を始めて7年になります。ロボットのハードもソフトもやってきましたけど、ロボットの自律安定性や、いま課題になっている計測ソフトのところで貢献できればいいなと思います」
目指すのはロボットを使ったシステム作り
サンリツの点検ロボットは、実際の道路での排水管走行はすでに20回以上を数える。
砂で小さなダムができている、生活汚水やゴミが溜まっている、非常に柔らかく深い泥溜まりがある──その度に出くわす、過酷な環境に1つ1つ対処してきた。
ある日、排水管試験中にロボットが管内で止まり、取り出すために三浦貴彦が臭く汚い排水管に這って入るハメに。その泥まみれの回収経験を2度と繰り返したくないと、チーム全員で走破性と信頼性を上げてきたという、冗談のような本気のエピソードもある。
2020年には“ロボット販売”が始まり、さらに進化は続いていく。だが、目標は、点検ロボットの“完成度”ではないと高倉は言う。
「目指しているのは、あくまでも設備の“点検システム”です。定期的に点検をして、経年変化を読み取り、補修が必要な場所と時期を事前に探り出す。そんなシステムに育てていきたい。ロボットは、その要素の1つです。
点検ロボットを出発点に、ロボットシステム・インテグレーターとしての経験を積んでいくことで、社会インフラや生産設備の現場に向けて、ロボットを活用したさまざまな形のプラットフォームが作れると考えています」