「高性能な設計」だけでは終わらない
過酷な現場で動かすまでが「開発」です
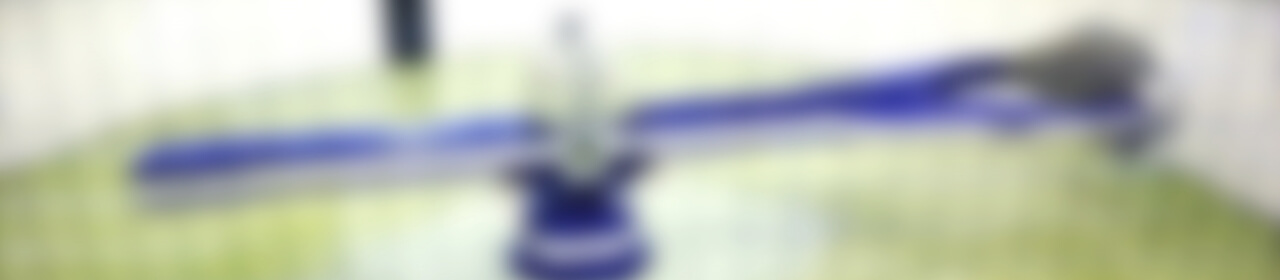
航空宇宙の開発は試験、また試験
Page.1
Page.2
航空機部品の開発は、特殊な試験の連続
宇宙向けと並んで、航空機用の部品もまた、非常に厳しい評価試験をクリアしなければならないジャンルだ。
2016年に、サンリツが受けた航空機用の部品開発では、数多くの評価試験を繰り返しながら、完成に漕ぎ付けた。
製作を依頼されたのは、開発中の航空機に使われる耐雷ケーブル。機体の発電系を制御するコンピュータ、GCU(Generator Control Unit)を接続するためのケーブルだ。
航空機には、飛行中に落雷で被害を受けることがないように、飛行機能の維持に関わる装備品は、最上位の耐雷性能が求められている。しかし、開発中のその航空機では、GCUの耐雷性能が不足していることが判明した。航空機に長く使われてきた実績があり、故障リスクが低い“枯れた”GCUそのものを変更するのは難しい。そこで、接続ケーブルの工夫で被雷時の電圧を抑え、耐雷性能を確保できないかというものだった。
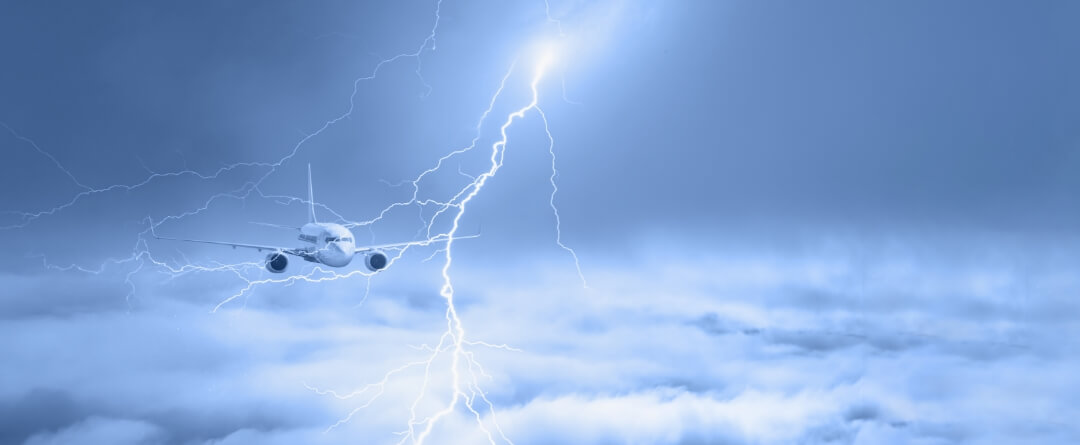
担当した開発四部の主任技師、箭原正道が語る。
「開発するケーブルそのものには、問題解決のアイデアを持っていましたし、技術的に、そんなに難しくはありませんでした。しかし、航空機の部品には、非常に厳しい、いくつもの基準があって、すべてをクリアしなければなりません。部品の開発そのものよりも、評価試験のほうにはるかに大きなエネルギーが必要でした」
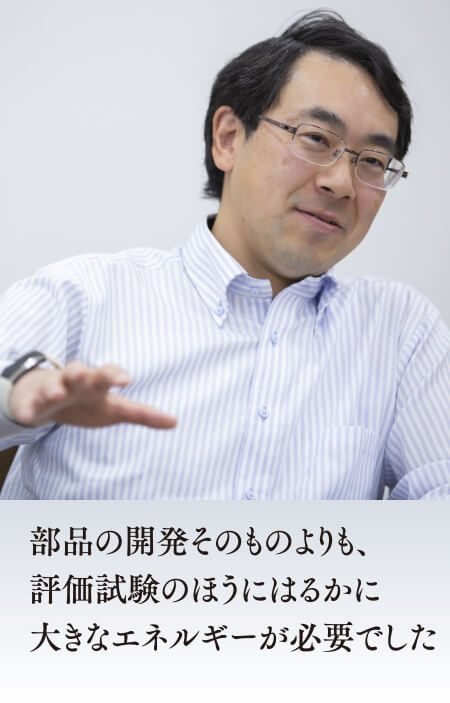
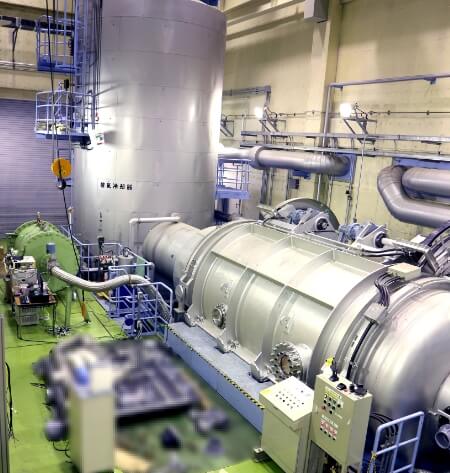
航空機の機体を空へ飛ばすには、国際的なルールが決まっている。
機体はもちろん、個々の装備品(部品)についても設計が所定の安全基準を満たし、なおかつ耐空性要件に適合することを、図面・解析書等の検査、静荷重・動荷重試験、耐火性試験など、数多くの試験を通じて証明することが求められる。
耐空証明には、すべての装備品に課せられた確性試験に合格しておく必要がある。
耐空証明を持たない機体は、空を飛べない。
しかも、その装備品を製造する工場は、航空宇宙分野のISO認証である「JIS Q 9100」の認証工場でなければならない。そもそもサンリツは、開発型のファブレスメーカーであり、自前の工場を持っていない。日常的に生産委託をするパートナー企業の中には、JIS Q 9100の認証工場はなかった。
開発期間も短く切られていたことから、航空機部品の経験豊富な企業に組んでもらい、自分たちのアイデアを形にする道を選んだ。
しかし、それでも、数々の試験は自分たちの手で行わなければならない。試験の大変さは、箭原が想像した以上だった。
「温度試験やEMC試験は、日ごろの私たちの開発でも行っています。でも、航空機部品には、かなり特殊な試験が必要になります。
例えば、“急減圧試験”という項目があって、15秒間で真空状態にまで減圧し、正常に動作するかどうかを確認する。GCUは、客室床下の与圧エリアにあるので、機体の損傷で急減圧が起きた時を想定しています。
“連続加速度試験”というのもあって、一般的な加速度試験と違い、9Gで3秒以上の加速状態を続けていく。
“燃焼性試験”は、一般の製品なら自己消火性のある素材を使っていればそれでOKなのですが、航空機部品の場合は、わざわざ実際に燃やして証明しなければならない。とにかく、初めて経験する試験ばかりでした」
試験できる場所がない!
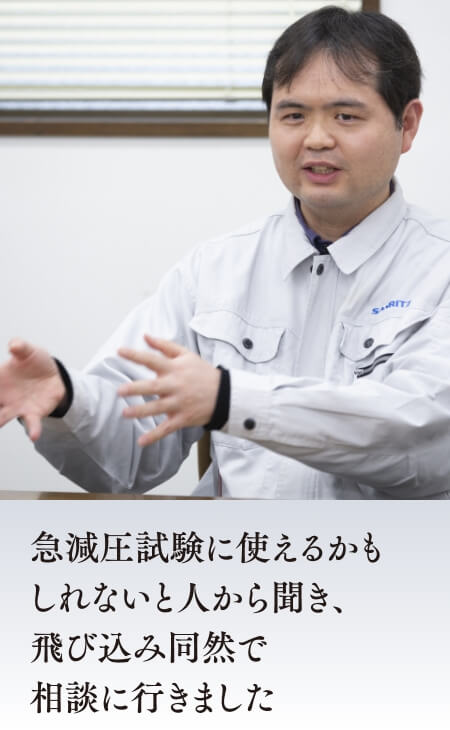
試験の大変さにも増して苦労したのは、試験ができる場所を探すことだった。戦後、日本では航空機開発がほとんど行われてこなかったことから、実験施設の数はかなり限られている。そもそも15秒間で真空状態にできるような実験施設など、どこにもない。米国なら設備一式が整った施設があるが、行く余裕はなかった。
開発チームで実験施設を探して奔走した生産技術部QCグループの主任技師、木須信崇はこんな体験をした。
「JAXAの調布航空宇宙センターにある実験設備が、急減圧試験に使えるかもしれないと人から聞き、飛び込み同然で相談に行きました。
大気が薄い高高度の環境を再現して、航空機エンジンをテストするための巨大な[高空性能試験設備]があるのですが、実際に訪ねてみると急減圧の機能はない。でも、試験の内容を説明するうちに、先方の研究者が、倉庫に置いてあるタンクを臨時に接続して、一気にバルブを開けば、急減圧の状態が作れるかもしれないとアイデアを出してくれたんです。
実際、その方法で、試験を行うことができました。臨時のタンク設置だけでも、大ごとでしたけど」
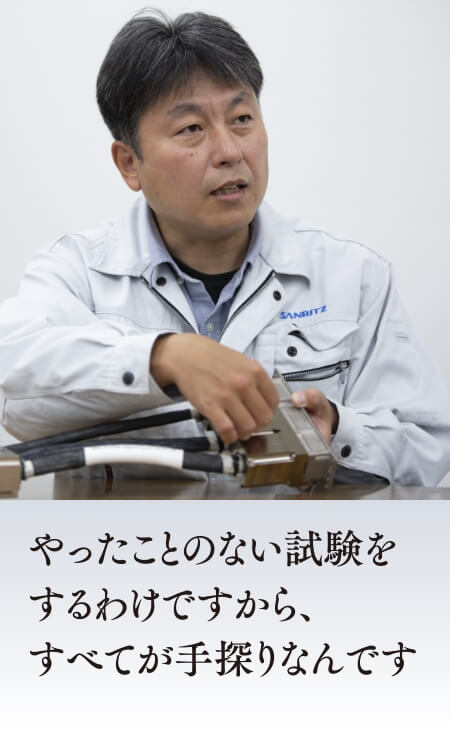
開発チームに参加していた開発一部の主任技師、瀬口英樹は連続加速度試験が記憶に残っている。
「違う用途で作られた施設を使い、やったことのない試験をするわけですから、すべてが手探りなんです。連続加速度試験では、巨大なアームが回転する設備を借りました。
耐雷ケーブルは小さいですから、回転中に飛び出して設備を壊してはいけない。アームの先には、自分たちで設計した治具を取り付けて、きちんと3軸方向それぞれの加速度試験ができるよう工夫しました。試験そのものより、準備に長い時間と労力とをかけた印象ですね」
必要なすべての試験をクリアし、あとは試験機に組み込み、米国での飛行試験に臨むだけとなった耐雷ケーブルは、想定外のあっけない幕切れを迎える。耐雷ケーブルの開発を知った米国の GCU メーカーが、急遽、GCU本体の耐雷性能を改善する設計変更案を提示してきたのだ。結局、サンリツの耐雷ケーブルは試作品に終わった。
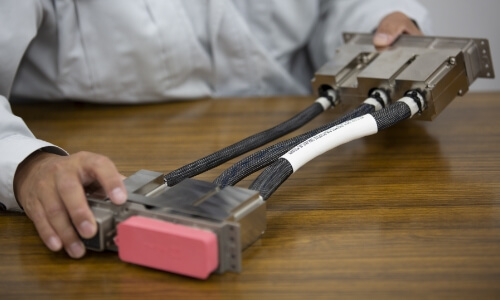
非常に残念な結果ではあったものの、開発チームに後ろ向きの感慨はない。初めての航空機分野に挑戦し、貴重な経験を数多く積むことができたからだ。技術力は、経験値の集積でもある。このスキルを活かせる次のチャンスを、チームメンバー全員が待ち構えている。
航空宇宙の開発は試験、また試験 Index
Page.1
Page.2