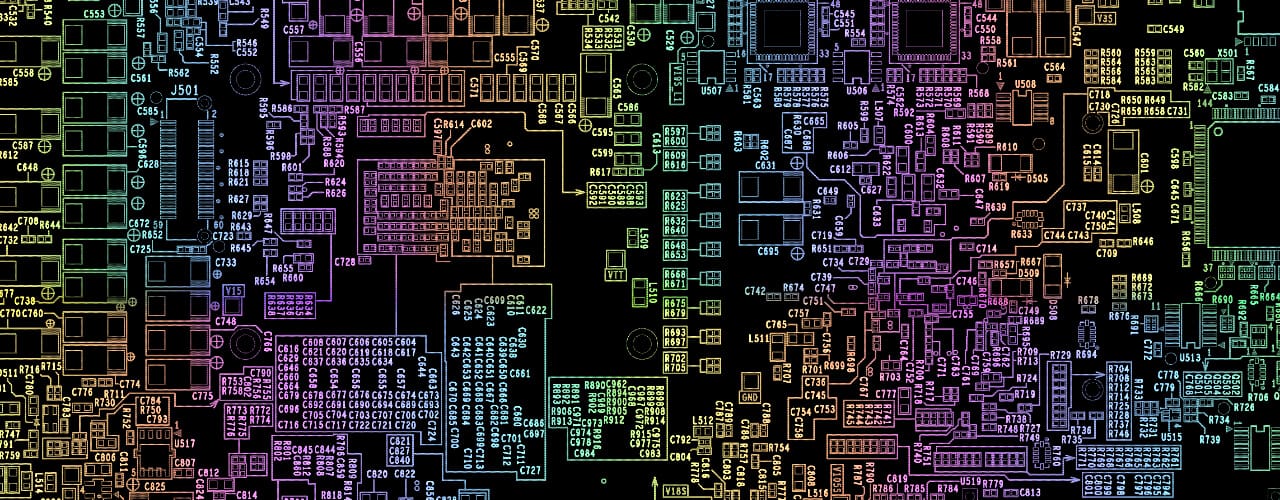
パートナー企業と一緒に品質を追求
- 仕事
- 働き方
ファブレスメーカーだけど
製造現場との近さでは負けません
サンリツオートメイションは自らの製造工場を持たない、いわゆる「ファブレスメーカー」だ。自社の経営資源のほとんどを製品の企画や開発にあてられる、市場の変化にフレキシブルに対応しやすい、独自の高い製造技術を持つパートナー企業と組むことで高品質な製品が作れる、等々──数多くのメリットがあることから、ファブレスは、世界的にも多くの技術先行型、製品企画先行型の企業が採用している方式である。しかし、ファブレスのメリットを生かすには、パートナー企業との密接な意思疎通が不可欠。まさにそこが、製品の品質を左右する要でもある。
Page.1
Page.2
不良品の原因究明に1年
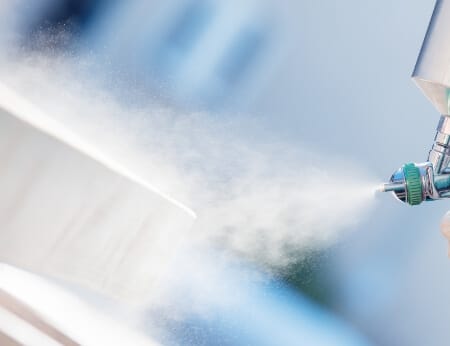
ある時、生産技術部主任技師で品質管理チームリーダーの村上龍太郎は、パートナー企業から納品されてくる製品に、繰り返しわずかな傷が発生していることに気が付いた。
「箱モノの製品だったのですが、しょっちゅう筐体の同じ場所に、数ミリ角の大きさで塗装ハゲが発生するんです。これは、サンリツの社内基準からするとNGなので、製造委託先にお願いして検品を強化してもらいました」
しかし、それでも発生は収まらない。村上は、製造委託先の工場へ出かけ、原因を探して工程をチェックしていったという。結局、見つかった原因は、予想もしていないものだった。
「塗装工程では筐体を全面塗装した後で乾燥をかけますが、吊り糸のようなもので吊って乾燥させていたんですね。その糸が揺れて、生乾きの筐体に接触する。触れた部分の塗装が弱くなって、乾いた後にパリンと剥がれ落ちていた。全面塗装を乾燥させるには、吊るしか方法がないので、一旦、乾かした後で、接触した場所を重ね塗りするという方法で対策せざるを得ませんでした」
一見、委託先の製造工程の問題のようだが、こうした不良の発生は、サンリツの側の工夫で防止できると生産技術部長の島村健司は言う。
「設計の側が、製造工程をもっと知っておくべきでしたね。全面塗装をしたら、下に置いて乾かすわけにはいきませんから、吊らざるを得ない。筐体に吊るための穴を用意しておけば問題ないですけど、そういったことが設計に織り込まれていなければ、製品のどこかの穴を利用して便宜的に吊ることになる。それが不良を生む要因になります。
そもそも全面塗装でなければ、吊らずに乾かすことができますから、本当に全面塗装が必要なのか、設計段階でそこから考えなければなりません。塗装に限らず、設計の中に製造プロセスを見越した要素を組み込んでおくことが、製品の品質を上げるには大事なのです。
ちなみに、メッキの工程はさらにシビアで、数ミクロンのメッキ厚の違いで不良になることさえある。設計する側がメッキ工程をよく分かっていないと、精度の高い製品にはなりません」
またある時は、製造委託先から納品されたプリント基板の配線にクラック(亀裂)が見つかったことがある。
その原因究明で、品質保証部副部長 兼 生産技術部副部長の久保雅史は、きちんとした手順を製造委託先と取り決めておくことの大切さを痛感した。
「その時は、製品の電源が動かないという現象が出ました。プリント基板を薄く切って、断面を顕微鏡で調べたりした結果、電源制御基板の配線にクラックが見つかりました。基板を作る際に問題があったのか、実装の工程で問題が発生したのか、あるいは別の問題があるのか、原因を探して製造工程を順にたどっていくと、ハンダ付けの工程に問題があることが判明しました。ハンダ付けは手作業で行っていたのですが、部品にハンダゴテを当てる角度が、きちんと管理されていなかったんですね。そこまで突き止めるのに1年くらいかかりました。
もちろん、資格を持った人たちが作業しているのですが、それでもバラつきは避けられない。結局、手作業ではなく、ハンダ付けの工程を機械化してもらうことで対応しました」
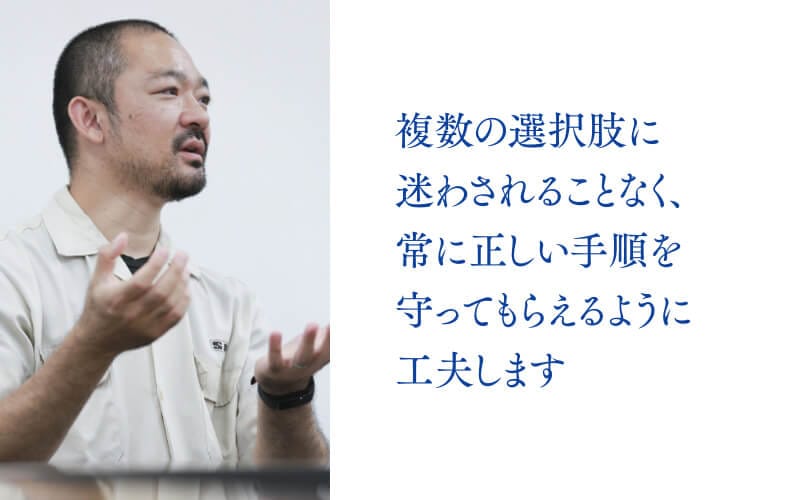
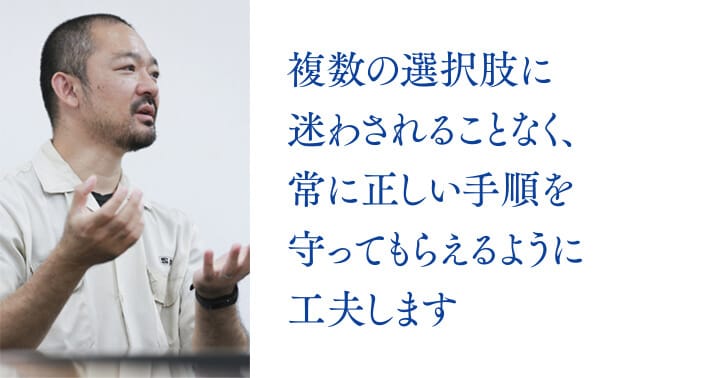
とは言え、機械化できない部分はどうしても残る。少量生産の製品は、そのための機械設備を用意することが難しいし、人が判断しながら進める工程もある。色や音などの官能検査も機械化にはなじみにくい。結局、人が作業する部分には、きちんとした手順を決めておくことが、品質確保の生命線であるという。
「手順を決めるにあたっては、作業者が、作業途中で複数の選択肢に迷わされることなく、常に正しい手順を守ってもらえるように工夫します。作業する人が変わり、熟練度が変わっても、同じ手順で作業してもらえれば、品質は変わりませんから」(村上)
手順を全て“見える化”する
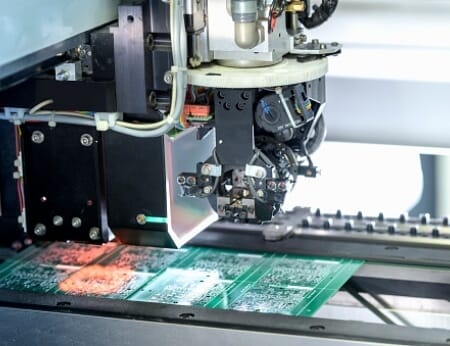
製品の不良を未然に防ぐためには、あらかじめ現場どうしの情報共有をしておくことが非常に重要だと、久保は言う。
「製造委託先とは、品質会議を開いています。ここを通して、例えば組み立ての委託先でしたら、組み立ての手順、検査の手順などを漏れなく規定するような文書を作ってもらいます。会社によって文化が違うので、すんなりとは行かない場合もありますが、粘り強く交渉して“見える化”し、共有するようにしています」
文書で共有するだけではない。実際にエンジニア同士が顔を合わせて情報を共有するようにもしている。
久保が続ける。
「新しい委託先企業を選定する際には、サンリツ社内で関連する技術のエンジニアに参加してもらい、先方の品質システムや製造現場をじっくり見て判断するようにしています。
これは、サンリツのエンジニアにとっても、非常に勉強になります。製造工程をつぶさに見ることで、どういう設計をすれば、高い品質のものを効率よく作れるのか、品質を落とさずにコストダウンできるのかを、具体的に知ることができます。こちらから製造内容を指示するだけでなく、先方のエンジニアから教わることがたくさんあるんですね。そうしたやり取りの中で現場同士の距離が近くなります。あらかじめ、意思疎通しやすい関係を構築しておくわけです」
しかも、意思疎通の相手は、直接のパートナー企業だけにとどまらない。
生産技術部スペシャリストで生産技術グループリーダーの山本順洋は、以前のように目の前のパートナー企業だけを見ていては品質確保ができないと感じている。
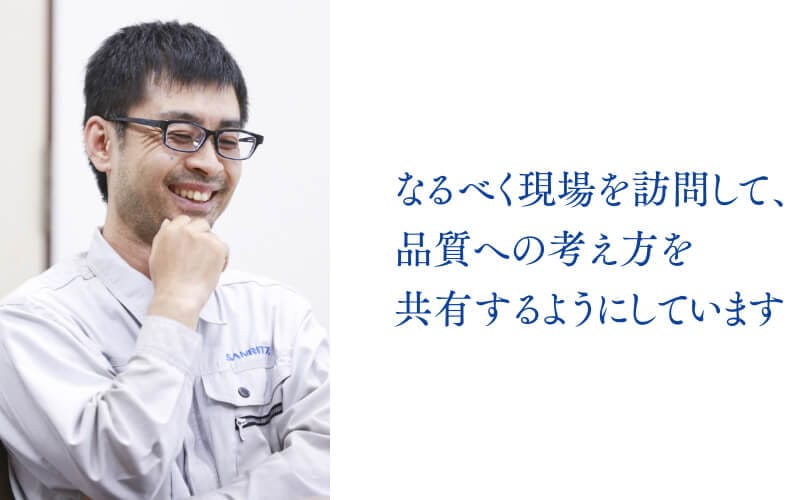
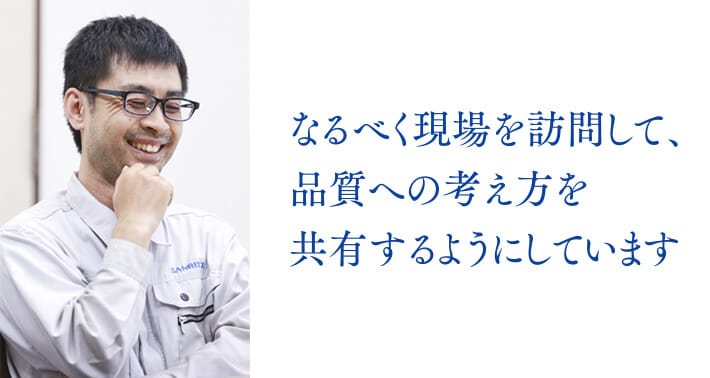
「以前のサンリツは、製品の大半がボードコンピュータでしたから、実装を委託するパートナー企業だけを見ていれば十分でした。ボード製品は製造技術が確立していますし、ある程度は委託先に任せられる環境があります。
しかし最近は、箱モノをはじめとして製品の幅が広がり、製造工程の一部が、委託先企業から、さらに別の企業へと再委託されるといった案件が増えています。再委託先をたどっていくと、ご夫婦2人だけでやっているような職人さんの工房があったりもします。図面もあまり整備せず、まさに職人の経験と勘で仕事をされているんですね。サンリツが委託している窓口のパートナー企業も、なかなか仕事のやり方に口を挟めないでいる。
でも、製造にかかわっている全ての人々が、同じ情報を共有し、同じ意識で仕事をしていただかないと品質は確保できません。ですから、なるべく現場を訪問して、手順などを文書で“見える化”してくれるようにお願いし、品質への考え方を共有するようにしています」
Page.2