災害で突然発生した生産危機は
全部署が連携し、臨機応変に切り抜ける
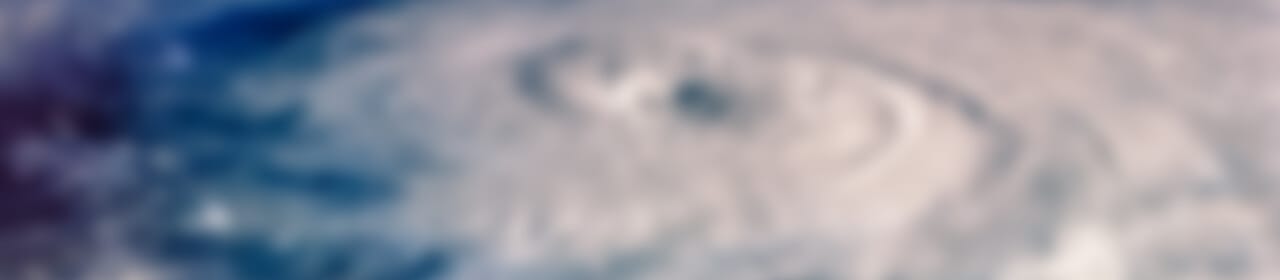
緊急事態を乗り切る
Page.1
Page.2
お客さまの「デッドライン」を守れ
こうした状況で、顧客への悪影響をいかに最小限にとどめるか。社内では、部署を越えた真剣な議論と、各部署が果たすべき役割の調整とが繰り返し行われていた。
生産管理部主幹で計画グループリーダーの坂 寛美は、そうした調整役を担った1人だった。
「毎週のように対策会議を開いていました。営業がお客さまに逐一状況を説明し、基板材料が変更になる場合は、その旨を申請します。すると、お客さまのほうから、比較データがほしいとか、基材を変えた代替製品を評価用に出してほしいといった要望が、営業担当を通じて寄せられます。お客さまによって要望の内容は色々です。
それら全部を把握した上で、品質保証部ではこの基材に対してはこういう評価が必要だとか、開発部はこういう試験環境で評価を行うとか、生産部門では、生産を管理し、検査が終わりしだいすぐに出荷できるよう、人員やスケジュールを計画するとか、とにかく毎週、各部門が情報をやり取りし、最速で納品できるよう調整していきました」
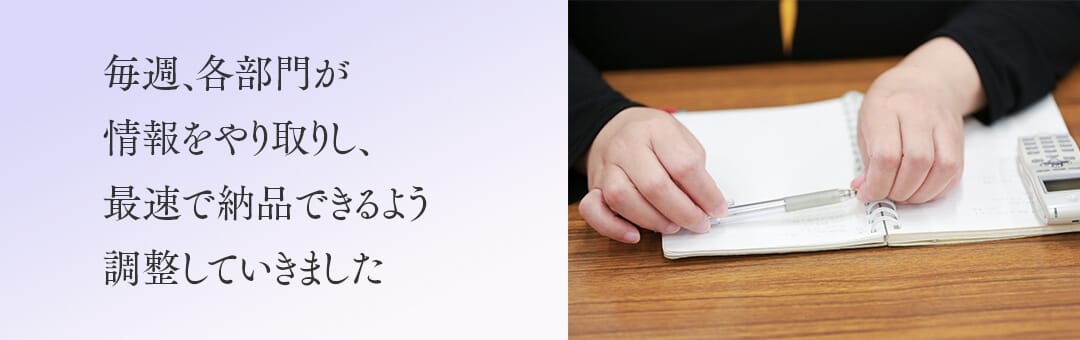
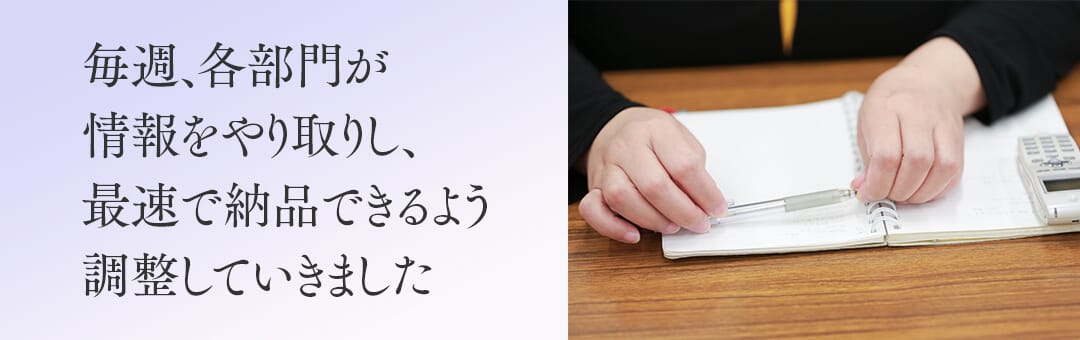
しかし、業界の混乱は収まらず、予定通りサンリツにモノが入ってこない、あるいは予定外でモノが入ってくるといったことが頻発。毎週の対策会議は、調整のやり直しに追われることとなった。
「突然、供給が止まるという事態は、部品レベルではたまにあります。ですから、全く未経験のオペレーションではありませんでしたが、この件は、影響するお客さまや製品の数といい、事態が収まるまでの期間の長さといい、規模が違い過ぎました」(坂)
顧客とのコミュニケーション窓口である営業部にも大きな負荷がかかった。
営業担当は、毎週の対策会議から必要な情報を抜き出してレポートを作り、いち早く顧客に伝えるようにしていた。いい情報も、悪い情報も、早く正確に伝える。互いの信頼関係なくして、一緒に危機を乗り越えることはできないからだ。
営業部主任で業務推進チームリーダーの森 ゆりかは、大混乱の中でも、全社で目指すところは明確だったと言う。
「最も重要だったのは、刻々と変わる状況を、情報としてお客さまと共有すること、そして、お客さまそれぞれのデッドラインを正確に把握することでした。
材料の供給がストップした時点でもいくらかの在庫はあったわけですから、このお客さま向けの製品はいつまでは供給できて、いつからストップする。ストップした状態で、いつまで耐えられるのか。代替品を用意するとなると、先方の評価試験も含めてギリギリいつまでには必要か、といったお客さまごとの事情を集約し、対策会議で調整して、確実にデッドラインを守ることが最優先でした」
幸いにも、特殊な仕様変更があった1社を除いて、結果的に顧客のデッドラインを割り込んだケースは1件も出なかった。
本来であれば、基板の材料変更も含めて、産業用コンピュータの仕様変更に対する顧客の抵抗感は非常に大きい。しかし、事態が事態だけに、ほとんどの顧客に前向きな対応をしてもらえたことが、土俵際ギリギリで持ちこたえられた大きな要因となった。
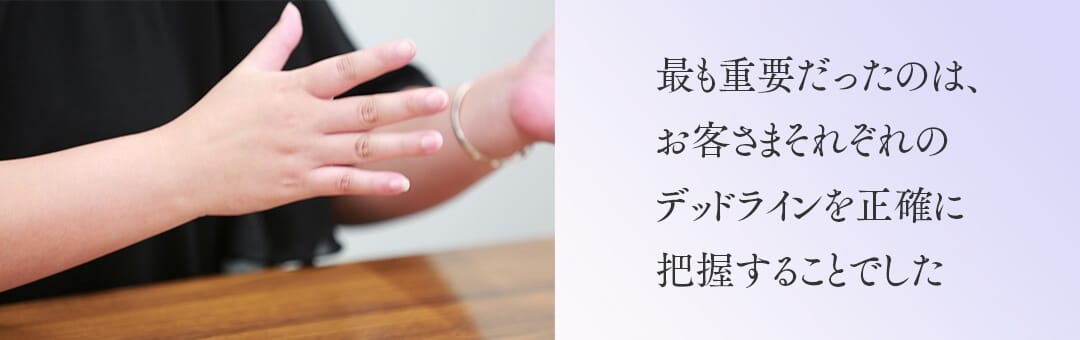
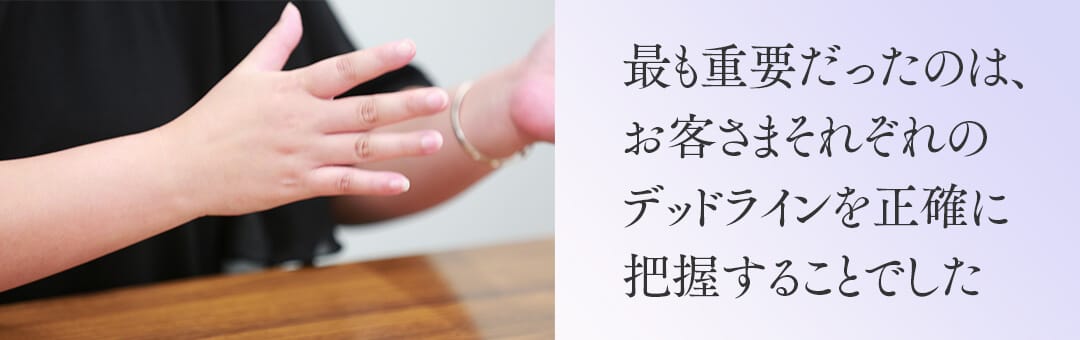
コンデンサが調達できない!
実は、サンリツが大規模な資材の供給不足に直面したのは、基板材料が初めてではない。2017年には、突如としてコンデンサの調達ができなくなるという事態が発生した。
それは前触れもなく、いきなりだったと渡邊は言う。
「コンデンサを供給している国内メーカーは数社ありますが、サンリツはそのうちの最大手から調達していました。ところが2017年末くらいに、サンリツで調達しているチップコンデンサを廃止にすると、突然、通告があったんです。
実際に廃止になるのはまだ先のことなので、それまでに代替品を手当てしようと考えていたら、通告から先の供給が事実上ストップしてしまった。発注をかけても、納期は360日以上先というあり得ない回答でした。それまで、コンデンサの納期は30日くらいでしたから」
ちょうどその頃、自動車のIT化・EV化、スマートフォンの高機能化、IoTの普及開始などが重なり、世界的にコンデンサの需要が急増していた。コンデンサメーカーとしては、その需要に対応するために、供給分野を選別したということのようだったが、サプライチェーンとして互いの信頼と責任を重んじる日本企業の商慣習からすると、いきなりの供給停止はあり得ないことだった。
「コンデンサを使っていない製品はないくらい、サンリツにとってコンデンサは必需品です。すぐに他の国内メーカーに当たりましたが、同様の引き合いが殺到していて、既存の取引先を守るのに手いっぱい。新規取引は受け付けてもらえない。結局、海外メーカーの製品に目を向けざるを得ませんでした」(青山)
しかし、海外メーカーの製品は、品質への不安が否めない。実際に取り寄せて確かめてみると、問題あるものが少なくなかった。
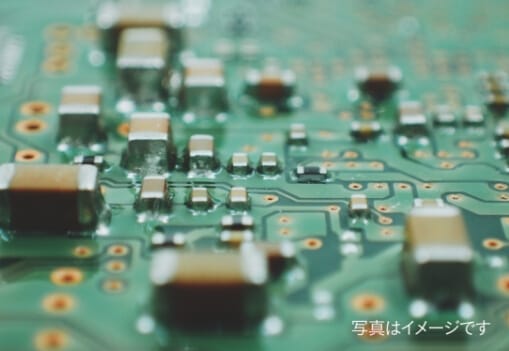
「コンデンサを縦に切って断面を確認すると、明らかにこれまで使っていた国産品と品質が違う。断面から見える中身の密度が低くて、スカスカしているんです。
品不足で市場価格が10倍くらいに跳ね上がり、そのうち、中国製に国産メーカーのラベルを貼ったニセ物まで出回るようになる。サンリツでも、掴まされかけたことがありました」(青山)
結局、この供給不足の時も、サンリツは顧客と情報を共有した上で、悪影響を最小限に抑えながら、コンデンサのメーカーや、使用するコンデンサの規格そのものを変更していく道を選んだ。
「これまでのコンデンサが手当てできない分は、国内外のメーカーのコンデンサを一時的に使う、容量や耐圧の違うコンデンサでも大丈夫なものは一時的に置き換える、ある程度の規格の継続性は確保した上で、違う部品を使った開発を進める、といった形で調達に問題のない製造体制が出来上がるまでの間をつないで行きました」(渡邊)
だが、世界的な品不足はいまだに解消せず、調達するには以前より時間がかかる。加えて、2020年のコロナ禍で、アジア各地の部品工場が止まり、むしろ調達環境が悪化した期間もあった。サンリツとしては、当面の在庫を多く持つことでリスクヘッジを行った。
しかし、それだけでは十分ではないと青山は言う。
「これからもさまざまなアクシデントが突発的に起こり得るわけで、在庫を持って備えるというだけでは不十分だと思います。アクシデントが起きた時に、すばやく臨機応変に動けるよう情報を整備することが重要です。
基板材料の一件以降、まずはサンリツ仕様の部品等が製造元でどう作られているのか、製造工程を確認して、詳細な情報を蓄積しています。何か起きてから情報を集めるのではなく、起きた時には該当する情報をデータベースから抜き出せばいいようにしました。数が多いですが、次は一般部品にも広げていきます。
十分な準備さえしておけば、社内には、お客さまへの供給責任を最優先する文化がありますから、部署関係なく即座に社内横断的にまとまって、普通では考えられないような変更にも柔軟に対応できます」
何があっても、顧客優先で社内が一致して臨機応変に動ける──その「柔軟性」こそがサンリツの強みなのである。
緊急事態を乗り切る Index
Page.1
Page.2