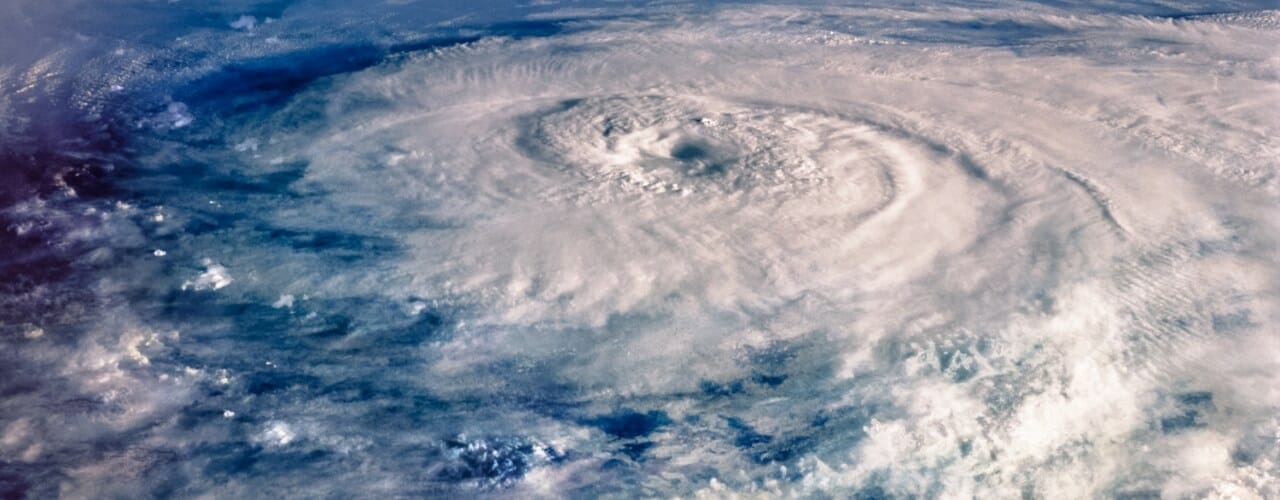
緊急事態を乗り切る
- 仕事
- 働き方
災害で突然発生した生産危機は
全部署が連携し、
臨機応変に切り抜ける
災害、疫病から政治・経済・社会の変異まで、現代は突然のアクシデントに満ちている。昨日まで順調な生産活動を続けていた企業に、ある日突然、災難が降りかかり、生産が続けられなくなることもある。その時、企業は、現場の人々は何を考え、どう動き、事態をいかに打開していくのか。企業としての価値観や文化が、最も顕著になる瞬間でもある。
Page.1
Page.2
台風で材料の供給が止まった!
2019年10月12日。
伊豆半島に上陸した台風19号は、東日本各地に甚大な被害をもたらした。
長野県で新幹線の車両基地が冠水したり、川崎市の武蔵小杉駅周辺でタワーマンションが水に浸かったりしたことは、まだ記憶に新しい。
福島県では阿武隈川が氾濫し、流域で広範囲な浸水被害が発生。郡山にある工業団地も水に浸かり、いくつもの工場が操業停止に追い込まれた。
郡山水害の影響は、サンリツオートメイションを含めた電子機器業界を直撃する。
プリント基板の材料を作っている国内最大手の工場が冠水し、生産が止まったからだ。
大手メーカーだけに、他の生産拠点でカバーできるのではと、最初は誰もが思ったが、同じ製品は郡山工場でしか生産していないことがすぐに判明。事態の深刻さは、またたく間に業界全体に伝わった。
生産管理部主任技師で調達チームリーダーの渡邊尚仁は、最初数日間のあわただしい動きを鮮明に覚えている。
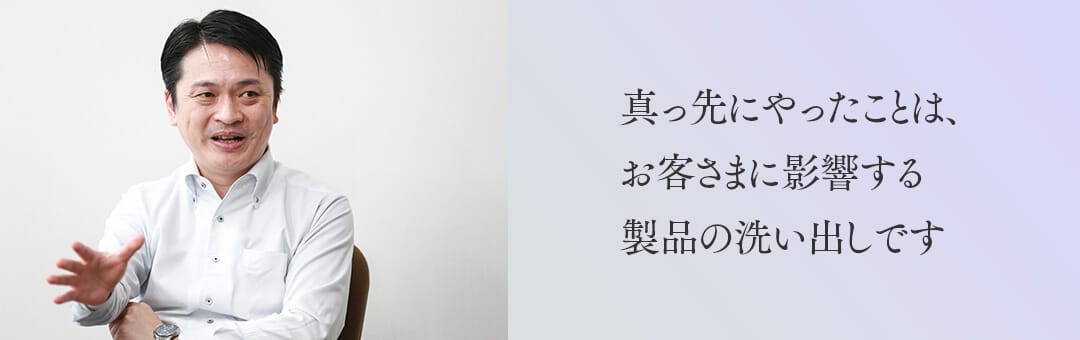
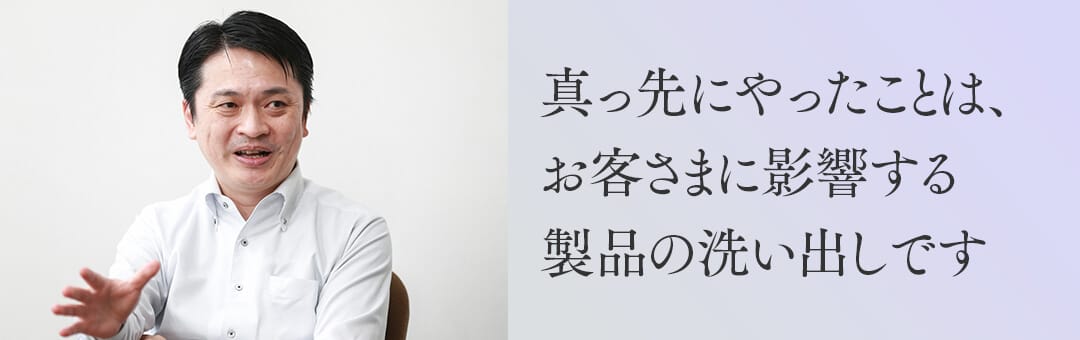
「鈴木社長の指示で真っ先にやったことは、お客さまに影響する製品の洗い出しです。リスト化してみると、ものすごく沢山ありました。台風が来たのは週末でしたが、週明けすぐに作業を始めて、水曜日にはほぼ全容が分かっていました。
サンリツが基板製造を委託しているメーカーは数社あって、そのうち最も多く委託しているメーカーは、製品の大半に郡山工場の材料を使っていました。
お客さまにはすぐに事態を連絡し、社内で対策を練りました。対策といっても限られていて、製造委託先に基板の材料を変更してもらうか、基板の製造委託先そのものを変えて、転注するかしかありません」
素人目には、ありふれて見えるプリント基板の材料だが、実際には非常にデリケートな性質を持つ。
生産管理部理事の青山光範は、基板材料は簡単には置き換えられないと言う。
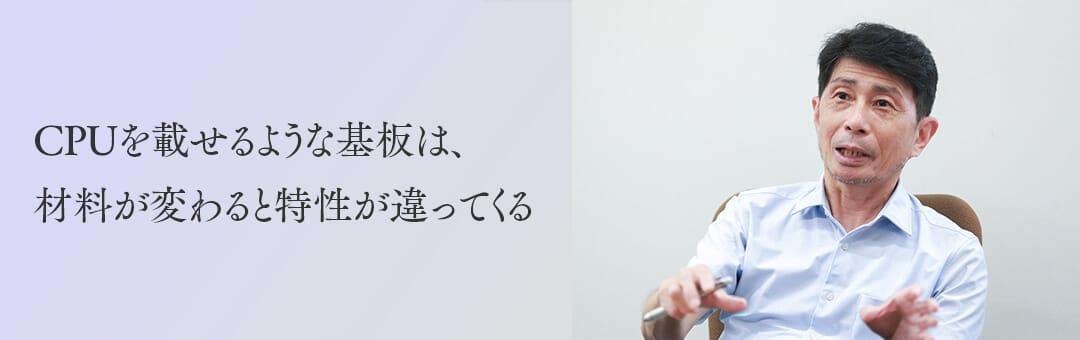
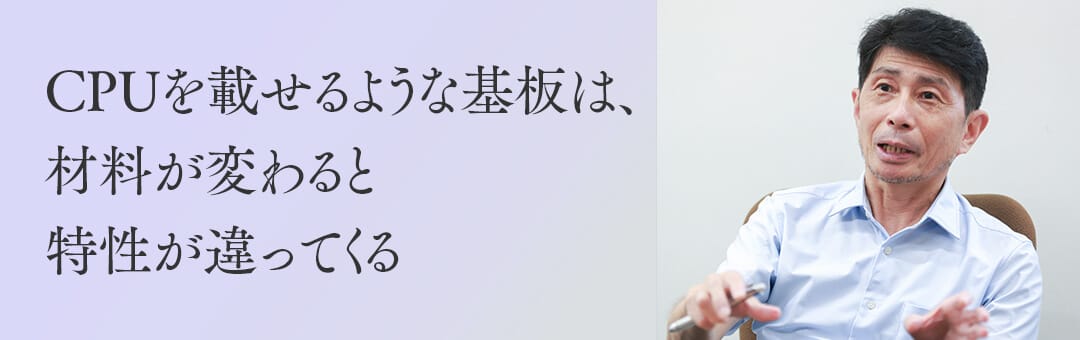
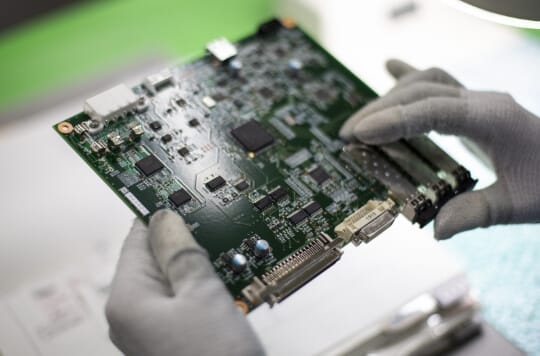
「CPUを載せるような基板ですと、材料が変わると特性が違ってきます。ですから、材料を変える際には、きちんと試験をして、問題がないことを確認しないと変更できません。委託先を変更するにしても、その製品には、やはり性能や品質の確認試験が必要です。どちらの方法を採っても、簡単に置き替えるというわけにはいかないのです」
しかも、長期保存ができないという基板材料の特性が、品不足をより深刻なものにしていた。
「基板材料には“消費期限”があります。長く置くと湿気を吸ったり、表面が酸化したりして、部品を実装するのに問題が出てきます。ですから、基本的には3カ月以内に使い切ります。再処理を施して延長しても6カ月が限度ですから、どこのメーカーも在庫は余分に持たないようにしています。当時、サンリツの委託先には2週間分の在庫しかありませんでした」(青山)
在庫が少ないので、材料の供給が止まると、すぐに生産をストップせざるを得ない。しかも、最大シェアを持つメーカーの供給が止まったことで、材料不足は日本中の電子機器メーカーに波及。基板材料の争奪戦が始まっていた。
郡山の工場はいつ再開するのか、基板材料は他のメーカーから調達できるのか、調達できたとして、それはサンリツの製品にうまく適合するのか、等々……あまりにも先行きが不透明なことから、サンリツとしては、基板の代替材料を探すこと、製造可能な新たな委託先を探すことの両方を並行して進めることにした。
同時並行で全部署が動く
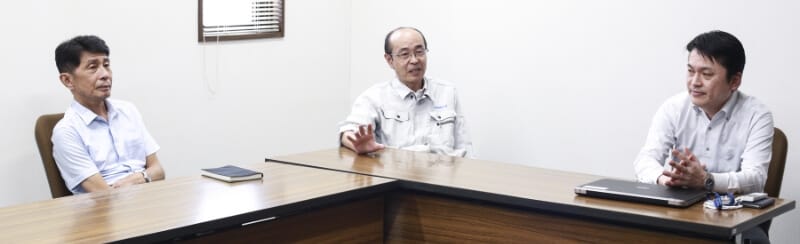
とにかく顧客に対する供給責任を最優先にする──
日ごろから当たり前になっている社内コンセンサスに基づき、営業は顧客対応、生産管理は代替材料や新規委託先の調査、開発は代替材料や新しい基板の評価、生産技術は代替製品の環境試験、等々、各部署が一斉に動き出した。
「本来の順番通りにやっていると時間がないので、全部を同時並行で進めました。代替材料は、国内の他のメーカーのもの、被災メーカーの中国工場のものを合わせて数種類が調達できました」(青山)
通常なら、基板材料は製造委託先の企業が選定し、サンリツが材料にまで関与することはない。出来上がった製品が、必要な性能・品質を満たしていれば十分だからだ。しかし、顧客への製品供給がひっ迫する緊急事態に、そんな役割分担に構っている場合ではなかった。
代替材料を調達できても、それが実際に製品に使えるかどうかは分からない。技術的な試験を経て、性能を確認する必要がある。
生産技術部長の島村健司がプロセスを説明する。
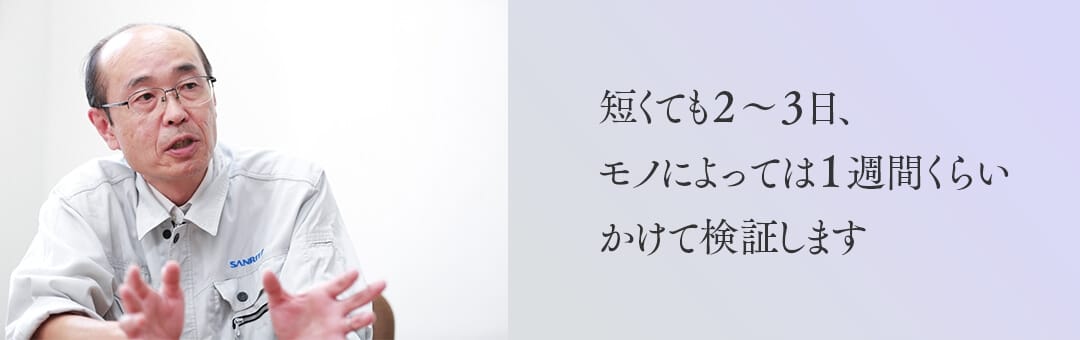
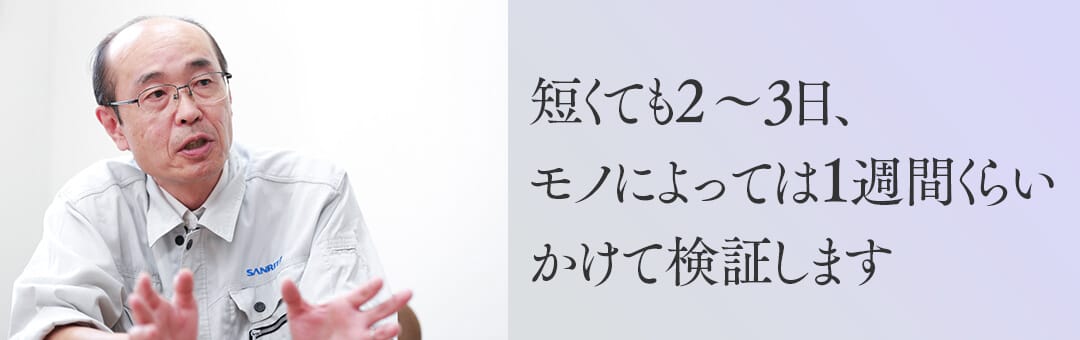
「代替材料を使っても、ある程度は弾性率や誘電率といったスペックを従来品と揃えることができます。そうやって基板メーカーが想定した“同等品”のパラメータを入手して、まず開発部が机上で内容を検証する。
次に、現物が上がってくると、温度試験、信号レベルの波形確認など、短くても2~3日、モノによっては1週間くらいかけて検証します」
しかし、確保したはずの代替材料も、現物がなかなか入ってこない。
代替材料の入荷を待ちながら、並行して、他の基板製造メーカーにも、同じ製品を発注することさえ行った。
「新しい製造委託先に作ってもらうと、その仕上がり品を試験するのにまた時間がかかります。代替材料を待つのとどちらが早いのか、その時は全く判断がつきませんでした。当初は3カ月くらいで収束すると言われていたものが、途中から半年はかかりそうな見通しになっていきました」(渡邊)
翌年の1月初旬になると、中国からの代替材料や、新規に発注をした製造委託先からの製品が少しずつ届き始めた。だが、数が全然足りない。しかも、市場に基板の供給が始まったことで、部品の実装を担当する工場には各メーカーから発注が殺到。製造がさらに遅れていくことになる。
Page.2